Vortex Flow Meter can be used for a wide range of fluids, i.e. liquids, gases and steam. They are to be seen as first choice, subject to verification to cover the requirements of a particular application.
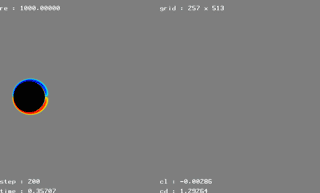
Vortex meters are essentially frequency meters, since they measure the frequency of vortices generated by a “bluff body” or ”shedder bar”.
Vortices will only occur from a certain velocity (Re-number) on-wards, consequently vortex meters will have an elevated zero referred to as the “cut-off” point. Before the velocity becomes nil, the meter output will be cut to zero. At a certain back-flow (above cut off point) some vortex meters could produce an output signal, which could lead to a false interpretation.
Vortex meters are actual volume flow meters, like orifice meters. These being intrusive meters like orifice meters, will cause the pressure drop as flow is increased, resulting in a permanent loss. consequently, liquids near their boiling point, could introduce cavitation as the pressure across the meter drops below the vapor pressure of the liquid.
As soon as the pressure recovers above the vapor pressure the bubbles will impede cavitation causes the meter to malfunction, and this should be avoided at all times.
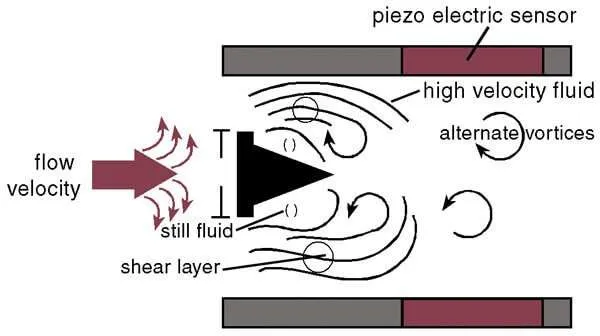
A fluid flowing with a certain velocity and passing a fixed obstruction generates vortices. The generation of vortices is known as Karman’s Vortices and culmination point of vortices will be approx. 1.2D downstream of bluff body.
Strouhal discovered that as soon as a stretched wire starts vibrating in an air flow, frequency will be directly proportional to air velocity,
St= f*d/V0 (without dimension), where:-
St= Strouhal’s number
f=frequency of wire
d=diameter of wire
V0= Velocity
This phenomena is called “vortex shedding” and the train of vortices is known as “Karman’s Vortex street”.
The frequency of vortex shedding is a direct linear function of fluid velocity and frequency depends upon the shape and face width of bluff body. Since the width of obstruction and inner diameter of the pipe will be more or less constant, the frequency is given by the expression;
f= (St*V)/c*D
f= vortex frequency, Hz
St= Strouhal’s number
V= Fluid velocity at the shedder bar, m/s
D= Inner diameter of the pipe, m
c= constant (ratio d/D)
d= Face width of shedder bar, m
The pressure loss gradient across the vortex meter will have a similar shape to that of an orifice meter. the lowest point in pressure will be at the shedder bar (comparable to vena contracta for orifice meter). downstream of this point of pressure will recover gradually, finally resulting in permanent pressure loss. To avoid cavitation, the pressure loss at vena-contracta is of interest.
The minimum back pressure required to ensure cavitation doesn’t occur is:
Pmin = 3.2*Pdel + 1.25*Pv
Pmin = minimum required pressure at five pipe diameters downstream of the flow meter in bar
Pdel = calculated permanent pressure loss in bar
Pv = vapour pressure at operating temperature in bar
Remember- for most vortex meters, d/D will have a range, 0.22 – 0.26, & the frequency of vortices will depend on the meter’s size, larger the meter, lower the frequency. So the maximum diameter of the vortex meter is restricted because the resolution of the meter could become a problem for control purposes.
To overcome this problem, on-board digital multipliers are used, which will multiply the vortex frequency without additional error.
Frequency Sensing Principle
Piezo-electrical Sensors- a pair of piezo-electrical crystals is built into the shedder bar. The shedder bar will be subject to alternating forces caused by shedding frequency will the piezo-crystals.
Variable capacitance Sensors- a pair of variable capacitance sensors is built into the shedder bar. As the shedder bar will be subject to alternating micro-movements caused by forces resulting from the shedding frequency, the capacitors will change their capacitance accordingly.
Selection and Sizing :
As the first step in the selection process, the operating conditions (process fluid temperature, ambient temperature, line pressure, and so on) should be compared with the meter specification.
The meter wetted materials (including bonding agents), and sensors should then be checked for compatibility with the process fluid both about chemical attack and safety. On oxygen, for example, nonferrous material should be used avoided or approached with extreme caution. The Vortex Flow Meter should then establish the meter minimum and maximum flow rates for the given application.
The meter minimum flow rate is established by a Reynolds number of 10,000 to 10,500, the fluid density, and a minimum acceptable shedding frequency for the electronics. The maximum flow rate is governed by the meter pressure loss (typically two velocity heads), the onset of cavitation with liquids, and sonic velocity flow (choking) with gases.
Consequently, the flow range for any application depends totally upon the operating fluid viscosity, density, and vapour pressure, and the application’s maximum flow rate and line pressure.
On low viscosity products such as water, gasoline, and liquid ammonia, and with application maximum velocity of 15 ft/s (4.6 m/s), vortex shedding meters can have a rangeability of about 20:1 with a pressure loss of approximately 4 PSIG (27.4 kPa).
The meter’s good (“of rate”) accuracy and digital linear output signal make its application over wide flow ranges a practical proposition. The rangeability declines proportionally with the increase in viscosity, decreased density, or reductions in the process’s maximum flow velocity. Vortex shedding meters are therefore unsuitable for use on high viscosity liquids.
Vortex Meter Advantages
- Vortex meters can be used for liquids, gases, and steam
- Low wear (relative to turbine flow meters)
- Relatively low cost of installation and maintenance
- Low sensitivity to variations in process conditions
- Stable long term accuracy and repeatability
- Applicable to a wide range of process temperatures
- Available for a wide variety of pipe sizes
Vortex Flow Meter Limitations
- Not suitable for very low flow rates
- Minimum length of straight pipe is required upstream and downstream of the vortex meter.
Vortex Flow Meter Applications
Vortex flow meters are suitable for a variety of applications and industries but work best with clean, low-viscosity, medium to high-speed fluids.
Some of the main uses include:
- Custody transfer of natural gas metering
- Steam measurement
- The flow of liquid suspensions
- General water applications
- Liquid chemicals & pharmaceuticals