The Precision Digital PDW90 Base Station is the starting piece to a rugged, customizable, point-to-multipoint wireless bridge. It offers a highly-flexible means of getting an analog, digital, or Modbus® signal from where you have it to where you need it. Modular input/output cards and expandable field units, available for the base station, and mean that the PDW90 can be customized to meet the needs of any wireless application.
The PDW90 is simple to order, simple to configure, and easy to trust with your application. A wireless survey tool is available for those installations that require a site survey for longer distances, making it easy to verify the setup will work the first time.
Field units accept analog, discrete, or Modbus® inputs and wirelessly broadcast it to the PDW90 base station. The base station can recreate these signals with its onboard RS-485 or analog and digital I/O cards. It can also be programmed to activate relays or output analog/digital signals to the field units. Just put the field units wherever there are process signals and the base station in the control room.
Fixed or remote antenna modules as well as a wide range of accessories are available, including mounting kits, antenna-related accessories, and repeaters. The antenna may be directly attached or remotely located. High gain directional antennae are also offered.
Application
The diagram below shows a typical PDW90 installation. Multiple transmitters are outputting analog signals to wireless field units. The analog signals are being wirelessly broadcasted to the PDW90 base station which then sends 4-20 mA signals to the destination devices.
Range: 500 ft (152.4 m) indoor, 1 mile (1.6 km) outdoor/line-of-sight)
PDW Manager Programming Software
Overview
There are no jumpers to set for wireless device input selection. Setup and programming of the base station is done using PDW Manager programming software. Setup of the wireless field units is done through either wirelessly through the base station using PDW Manager programming software or via direct USB programming with PDW Manager. The programming buttons located underneath the enclosure cover are for very limited programming options, such as network ID and Modbus address.
Programming the Base Station
The base station is programmed using PDW Manager programming software. PDW Manager can be found on the included CD or downloaded from www.predig.com/PDWManager. Once the software is running, power the unit using a 24 VDC power supply and connect the base station’s micro USB port to a PC using the provided USB cable.
Note: Base station must be powered externally prior to programming via USB.
The PC will automatically install the appropriate device drivers. Once this has completed, the device will appear in the Device list at the top of the PDW Manager window. Click Connect.
Connecting Field Units to Base Station
The first thing that must be done when programming the PDW90 is connect all of the wireless field units to the base station. Configuration of the base station is accomplished using the PDW Manager software, while the individual field units may be programmed using the device buttons which are accessed by unscrewing the enclosure cover.
After the base station has been connected to PDW Manager, field units can be connected to it from the Remote Unit Configuration tab. Select each unit from the Unassociated Remote Units list and click the Add to Client List button
Field units must have the same network ID and encryption settings as the base station in order to connect. Each field unit must be programmed to have its own unique Modbus address.
Note: All units must be powered on in order to connect them to the base station.
Base Station Configuration
The Base Station Configuration tab is where the base station name, network ID, password, and Modbus settings may be modified. Once you are finished modifying any of these settings, click the Save Settings button to write your changes to the device.
If you have made changes that have not yet been saved and would like to load the saved settings from the base station, click the Read Settings button.
Input/Output Module Configuration
The Base Station IO Configuration tab is where individual I/O modules connected to the base station may be programmed. Click on one of the installed modules in the IO Modules list to the left of the screen in order to begin programming that module.
Analog Inputs Module
Each Analog Inputs module has two input channels. Each channel may be independently programmed to accept either a 4-20 mA, 0-10 V, 0-5 V, or 1-5 V analog input. These channels may also be mapped to remote analog outputs or Modbus registers. Once you have modified the module’s settings, click the Save Module Configuration button to save these settings to the base station.
If you have made changes to the module that have not been saved and would like to load the saved settings from the base station, click the Read Settings from Hardware button. If you would like to reset the selected module to its default settings, click the Load Default Settings button.
The Monitoring area at the bottom may be used to view the current analog input reading or manually test analog input operation.
4-20 mA Analog Outputs Module
Each Analog Outputs module has two 4-20 mA output channels. Each channel may be independently programmed and mapped to remote analog inputs or Modbus registers. Once you have modified the module’s settings, click the Save Module Configuration button to save these settings to the base station.
If you have made changes to the module that have not been saved and would like to load the saved settings from the base station, click the Read Settings from Hardware button. If you would like to reset the selected module to its default settings, click the Load Default Settings button.
The Monitoring area at the bottom may be used to view the current analog input reading or manually test analog input operation.
Digital I/O Module
Each Digital I/O module has four I/O channels. Each channel may be independently programmed as either an input or an output. These channels may also be mapped to a remote digital I/O or Modbus register. Once you have modified the module’s settings, click the Save Module Configuration button to save these settings to the base station.
If you have made changes to the module that have not been saved and would like to load the saved settings from the base station, click the Read Settings from Hardware button. If you would like to reset the selected module to its default settings, click the Load Default Settings button.
The Monitoring area at the bottom may be used to view the current digital I/O state or manually test digital I/O operation.
Relays Module
Each Relays module has two channels. Each channel may be independently programmed and mapped to remote digital I/O or Modbus registers. Once you have modified the module’s settings, click the Save Module Configuration button to save these settings to the base station.
If you have made changes to the module that have not been saved and would like to load the saved settings from the base station, click the Read Settings from Hardware button. If you would like to reset the selected module to its default settings, click the Load Default Settings button.
The Monitoring area at the bottom may be used to view the current relay state or manually test relay operation.
Remote Unit Configuration
The Remote Unit Configuration tab is where connected field units may be programmed to communicate with the base station. Select a connected field unit from the Connected Clients list in order to begin programming that unit.
A field unit’s human readable name may be changed by clicking the Change Name button. Be sure to give each field unit a descriptive name, such as the location of the unit in your facility or the devices connected to it, in order to make future programming easier.
Analog Input
Each field unit’s analog input may be programmed to accept a 4-20 mA, 0-10 V, 0-5 V, or 1-5 V signal. Once you have modified the settings, click the Save Configuration button to save these settings to the field unit.
The IO Mapping section will show to what (if any) device the analog input has been mapped. The Monitoring section at the bottom may be used to view the current analog input reading or manually test analog input operation.
4-20 mA Analog Output
The 4/20mA Output tab is used to program the selected field unit’s analog output. Once you have modified the settings, click the Save Configuration button to save these settings to the field unit.
The IO Mapping section will show to what (if any) device the analog input has been mapped. The Monitoring section at the bottom may be used to view the current analog output reading or manually test analog output operation.
Digital I/O
Each field unit has four digital I/O channels. Each channel may be independently programmed as either an input or an output. Once you have modified the settings, click the Save Configuration button to save these settings to the field unit.
The IO Mapping section will show to what (if any) device the digital I/O has been mapped. The Monitoring section at the bottom may be used to view the current digital I/O state or manually test digital I/O operation.
Modbus
Each field unit is capable of transmitting Modbus® RTU communications. Enter the Modbus network settings on the Modbus tab in order to communicate with the Modbus network. The Modbus address must be unique in order to ensure field unit/base station connectivity.
Once you have modified the settings, click the Save Configuration button to save these settings to the field unit.
Advanced Configuration
Device communication can be secured by enabling 128-bit AES encryption. A channel mask may also be set for interference immunity. The encryption key and channel mask may be entered on the Advanced tab. Once you have entered the encryption information, click Save Settings. If you have made changes that have not been saved and would like to load the saved settings from the base station, click the Read Settings button.
The wireless field units must share identical encryption keys in order to communicate with the base station, so be sure to enter the same information for all of the field units.
If you would like to reset the base station to factory default settings, click the Reset all system parameters to Factory Defaults button. All field units may be cleared from the client database by clicking the Clear Client Database button.
Programming the Field Units with PDW Manager
The field units may also be programmed using the PC based PDW Manager. Field units connect to a PC via the micro USB connection on their face, underneath the enclosure cover. Use of PDW Manager is required for programming advanced settings such as wireless encryption and analog signal calibration. PDW Manager can be found on the included CD or downloaded from www.predig.com/PDWManager. Once the software is running, power the unit using a 24 VDC power supply and connect the device to the PC using the provided USB cable.
Note: Units must be powered externally prior to programming via USB. The PC will automatically install the appropriate device drivers. Once this has completed, the device will appear in the Device list at the top of the PDW Manager window. Click Connect.
The image below shows the available options on the Configuration tab while the field unit is connected. The network ID, Modbus settings, and password may be configured from this tab.
The devices’ analog inputs and outputs can be calibrated using the Calibration tabs. The IO Testing tab allows you to perform diagnostics and testing on the units.
Device communication can be secured by enabling 128-bit AES encryption. A channel mask may also be set for interference immunity. The encryption key and channel mask may be entered on the Advanced tab. Once you have entered the encryption information, click Save Settings. If you have made changes that have not been saved and would like to load the saved settings from the base station, click the Read Settings button.
The base station and field units must share identical encryption keys in order to, so be sure to enter the same information for the base station all of the field units.
Connections
Base Station
The diagram below shows the locations of screw terminal blocks on a fully loaded PDW90 base station electronics board. This diagram shows the board loaded with four relay modules, four digital I/O modules, four analog input modules, and four analog output modules. Actual module locations may differ.
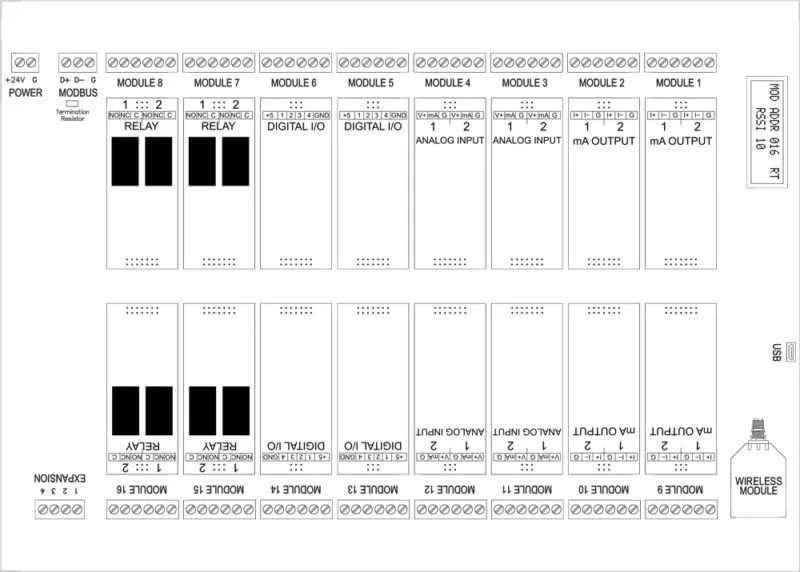
Mounting Dimensions
Base Station
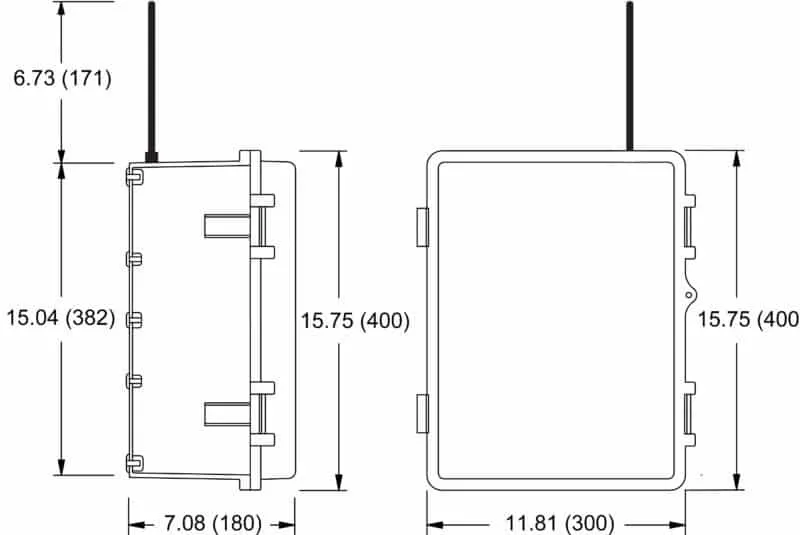