Introduction
There are several fundamental measurement techniques for flow meters, such as:
- Electromagnetic Flow Meters
- Thermal Mass Flow Meters
- Coriolis Mass Flow Meters
- Differential Pressure Flow Meters
- Vortex Flow Meters
- Position Displacement Flow Meters (PD Flow Meters)
- Turbine Flow Meters
- Variable Area Flow Meters
Other than the ones mentioned above, there are some less known unique types of flow meter technologies that often offer solutions for individual applications. There is no “Best Flow Meter”, all depend on the applications and what the user expects from the unit.
In this article, you will understand at measuring instruments for relatively low gas flows, from a few cc/min to 500 or 1000 ln/min, for example. In this application area is the gas mass flow meter with the thermal bypass concept the most common instrument. There are gas mass flow meters (MFM) and mass flow controllers (MFC). Eventually is a flow meter equipped with a control valve, and the you can provide a setpoint that determines a generated gas flow. MFCs is the reference to these instruments.
Measurement Concept
In the thermal bypass concept, most of the measured gas flow through a bypass. In the bypass is an element that generates a minimal pressure drop. As a result, a small quantity of the gas runs through the sensor, which runs parallel to the bypass. This sensor measures the gas flow, which is representative of the total amount of gas monitored. Each instrument built for specific gas and a particular range of measurement.

Mass flow meters (MFM) and mass flow controllers (MFC), the names speak for themselves: these instruments measure and regulate the gas flow, for instance, in kg/hr. The measured value can also be expressed in units of normalized volumes, such as ln/min (normal litre per minute) or SCFH (Standard Cubic Foot per Hour). In SCFH (Standard Cubic Foor per Hour)here the “S” refers to 20°C and 1 atmosphere, while NCCM (Normal Cubic centimetres per minute) with reference conditions as 0°C and 1 atmosphere. After all, there is a fixed relationship of gas in mass units versus normalized volumes (density).
There is a distinction between the MFCs based on a capillary sensor and instruments with a MEMS (Micro-Electro-Mechanical System) sensor. Both sensor techniques have advantages and limitations. The word “cons” is here deliberately avoided because there are no terrible measuring instruments. The application should drive preference example like Porsche 911 is a fantastic car, but you shouldn’t use it in the sand of the Sahara.
What is Capillary Flow Sensor?
The capillary sensor consists of a thin steel tube (0.2 to 1 mm o.d.) around which wrap with two thin platinum wires. The platinum wires act as electrical resistance and are part of a Wheatstone bridge. The resistance value of the platinum wire depends on the temperature. There is a current going through these wires, which heats them up. At zero flow is the resistance is the same, but when the flow goes through the sensor, there will be a difference in temperature that will be detected by the electronics.
Laminar Flow Element (LFE) equip in MFC with a capillary sensor in the bypass. This LFE creates laminar flow behavior, just like inside the sensor. The LFE means that the relationship between the flow through the sensor versus the flow through the bypass is almost linear over the measured range. Due to this linearity, it is possible to calibrate this MFCs with a cheap, pure gas like air and use a known factor to make the meter suitable for another exotic, explosive, poisonous or inflammable gas. If this so-called K-factor is applied, there will be additional uncertainties. In user manuals of renowned manufacturers are further indicative inaccuracies reported to more than 2%. Parameters such as viscosity, pressure, and temperature affect the accuracy of the K-factor. It is essential to take note of this traditional calibration method, which creates uncertainties which are not often mentioned in the documentation.
This type of MFM/MFC must be calibrated with the actual gas as used in the application. The advantage is that the instrument thereby is more accurate. For some exotic gases, a correlation is possible, although the repeatability stays very low, the accuracy will suffer.
What is MEMS Flow Sensor?
The MEMS-based MFM/MFC has no LFE but a regular by-pass. The function is to ensure a defined percentage of the total gas flows through the sensor. The bore of the sensor is much larger so that for example, the pressure drop is relatively low and the sensor less sensitive to pollution than a capillary. A MEMS sensor is also a lot more sensitive and due to that a turndown of 1000:1 is obtainable (versus 50:1 for capillary sensors).
The biggest advantage of the MEMS sensor is, however, that there is no (measurable) drift. Drift is a slow shift of the zero, and the measured value at a given flow hence affects the accuracy.

The Pros and Cons
Capillary sensors exhibit effects of mechanical and thermal stress on the Platinum wires and aging of insulation materials. The capillary sensors must receive a “burn-in” in heated cabinets to speed up the aging process. Aged Capillary sensors exhibit less drift than, but it is still there. The effect is sometimes hidden by the manufacturer with low-flow cut-off options. The test signal is forced to zero under a specific value so hide the small drifts.
The MEMS sensors consist of two or three temperature sensors and a heater, vapor-deposited as a microscopic molecular layer on a thin membrane. Conceptually the MEMS is sensor low-energetic, and due to the membrane thermally and stress isolated, this ensures that MEMS sensors are free of any mechanical and thermal stress. An additional plus point: the sensor is part of an electronic circuit all mounted on the MEMS. The measured signal digitalized immediately on the MEMS sensor itself. No bad connections, no EMC was distorting the signal. These are the main reasons why MEMS sensors are without drift and maintain long-term accuracy, reproducibility, and reliability.
Other advantages are that the sensor is very fast: 50 msec response time. When you power the unit up is ready for use within one second, while capillary concepts take 15 minutes). The instrument does not need the zero adjustments regularly (for capillary MFCs a standard routine). MEMS-based MFCs offer the significantly better reliability of the measured and regulated flow.
Finally, should not mention that the MEMS do need to be appropriately temperature-compensated. The more advanced manufacturers always calibrate their MEMS unit under two different temperatures. During operation, they measure the gas temperature and compensate the MFM/MFC readings. This also contributes to the accuracy and repeatability of the gas measurement/control.
Summary
Both concepts have their strong and weaker aspects. The capillary sensor, in combination with the LFE leads to a reasonably linear relationship between the flow through the sensor and bypass. Due to this, it is possible to use so-called K-factors, a multiplier factor between two gases. For corrosive gases, the capillary sensor can calibrate with a safe gas like air and apply this K-Factor. In this way, the units can measure reasonable correct with corrosive gas.
However the K-factors calibrations are not always accurate, some MFCs better than others, the best is still to calibrate with the real gas, although most capillary manufacturers not doing this. Other plus points are the availability of high-pressure versions and the choice of material for corrosive applications.
For the MEMS-based MFCs, we have better specifications when it comes to accuracy, response time, and turndown. MEMS sensor not possible to use of K-factors, hence the MFC need calibration with the real gas of the application. The restriction is that these MFCs not suitable for each gas. Some MEMS manufacturers go a long way to temperature compensate their units; this results in a better accuracy over a more extensive temperature range.
A crucial advantage of the MEMS-based MFCs is the zero drift in the sensor. That results in better long-term accuracy, repeatability, and reliability.
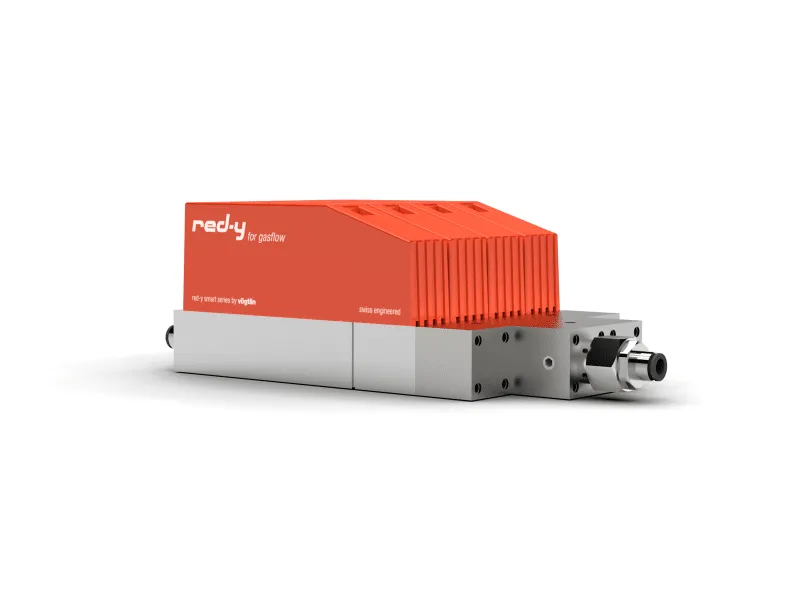