In the realm of Low-E glass manufacturing, vacuum magnetron sputtering stands out as a premier coating technique employed globally. Central to this process is the meticulous control of gas flow within a vacuum environment, achieved through the precise calibration of a high-performance mass flow controller (MFC). This critical control ensures the maintenance of a stable vacuum level essential for optimal thin film deposition on the glass substrate.
At the heart of vacuum magnetron sputtering lies the cathode, often represented by the magnetron target. A high voltage, supplied by either an AC or DC power source, energizes the process gas, typically a combination of reactive gases like O2 and N2 or inert gases like Ar, thereby initiating plasma generation. Within this plasma environment, electrons, propelled by the electric and magnetic fields, collide with gas molecules, leading to the formation of an abundance of positive ions and electrons.
With sufficient energy, these positive ions are directed towards the cathode target material. Upon impact, the target material undergoes sputtering, releasing atoms that subsequently deposit onto the glass substrate, facilitating the creation of thin films. Essential to the manufacturing process is the achievement of uniform and consistent film layers across the glass substrate.
To attain the desired precision, the mass flow controller plays a pivotal role in regulating the flow of gases within the vacuum chamber. This meticulous control ensures not only the stability of the vacuum environment but also the reproducibility and uniformity of thin film deposition onto the glass substrate.
In conclusion, the synergy between vacuum magnetron sputtering, precise gas flow control facilitated by the mass flow controller, and the deposition of thin films onto the glass substrate is paramount in the production of high-quality Low-E glass products.

Application
In Low-E glass manufacturing, vacuum magnetron sputtering is a common coating technique used across the world. In this process, gas flow (reactive gas O2 and N2 or inert gas Ar) in the vacuum environment must be controlled with a high precision mass flow controller (MFC) to maintain a stable vacuum level.
With the magnetron target acting as the cathode, a high voltage provided by an AC or DC power supply will ionized process gas to generate plasma. Electrons move at high speed under the joint force of the electric field and magnetic field, colliding with gas molecules and creating more positive ions and electrons.
After gaining certain energy, positive ions in the electric field will hit the cathode target material. The sputtered target material deposits on the glass substrate to form thin films. Uniform and consistent film layers are required.
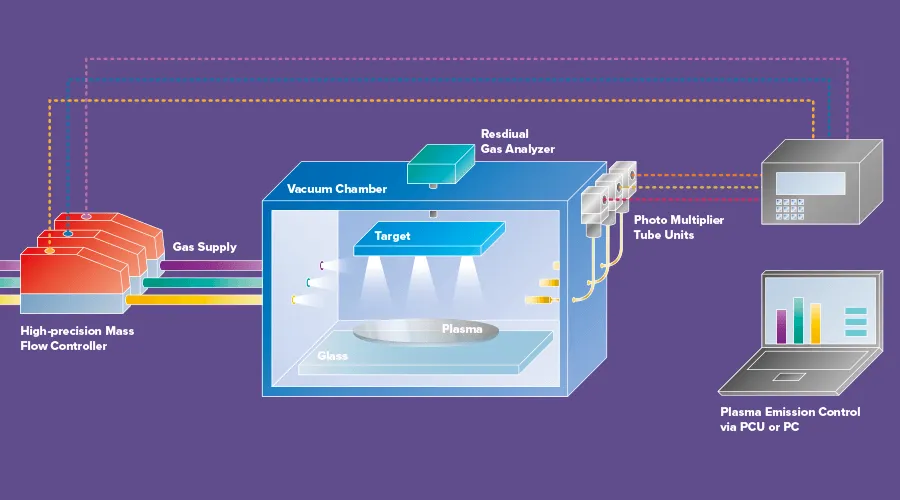
Challenge
In-flow gas should be maintained at a very stable level in the coating process to avoid uneven coating and significant spots and negatively impacting the overall energy of particles in the coating, which is not favorable for reactive deposition. A complicated gas distribution system requires numerous process gas branches. Installation and commissioning of single-channel gas circuits are tedious with the heavy workload. Also, this system typically reduces efficiency and generates multiple leakage points. Human operation errors (wrong connection of gas mixing and connection circuits) also can negatively impact operations.
Solution
MEMS sensor of the Mass Flow Controlers (MFCs) provides for a 350ms fast response. Plug-and-play functionality and no warm-up periods improve user productivity.
Vögtlin Mass Flow Controllers have a unique way of compensating for changes in ambient and gas temperature, which actively improves the repeatability. The MEMS technology ensures long-term stability without any drift as long as the gas supply is clean and dry.
An Integrated valve bank design and accurate internal mixing and distribution pipe design help avoid operational risks and improve end-user comfort. Other benefits include saving of consumables for gas source pipes, reduced leakages points and field installation time as well as an easy and accurate realization of complicated gas mixing and distribution process.
Units can be calibrated for multiple gases and parameters, which leads to significant reductions in spare part inventories and cost savings.
Key Features
- High repeatability & reliability
- Short response time
- Safe and fast control
- Compact unit with high-quality components
Interfaces
- Analog
- Modbus RTU
- Profibus DP-V0/DP-V1
- Profinet
- EtherCAT