For any magnetic flowmeter to function correctly, it must have three connections (including a ground) to the process liquid passed from the magnetic flow tube onto the magnetic flow transmitter. About 80 percent of the time, problems with the flow measurement readings provided by a magnetic flowmeter can be traced directly to improper solution ground connections.

A magnetic flow meter measures flow rate by sensing the force created within the magnetic flow tube based on Faraday’s Law. It has three connections: two electrode signal cable leads that pass from the magnetic flow tube’s measuring electrodes onto the magnetic flow transmitter and a signal ground (SG) connection.
The SG connection is critical for achieving a stable zero flow measurement reading consistently and providing accurate measurements during flow. It acts as a reference point for the measurement, and without it, there can be no confidence in the flow rate measurement.
There are two common causes of solution ground connection problems. The first is a missing SG connection from the process to the magnetic flow tube’s body/case. The second is a failure to pass the SG connection properly from the magnetic flow tube’s body onto the magnetic flow transmitter’s SG terminal.
Ensuring proper SG connection is essential for obtaining reliable and accurate flow rate measurements in a magnetic flow meter. Without it, the flow meter cannot function correctly, and the accuracy of the measurement will be compromised. It is recommended to follow the manufacturer’s instructions to ensure proper installation and maintenance of the magnetic flow meter’s SG connection.
Grounding Rings vs. Grounding Electrodes
To determine when to use grounding rings or grounding electrodes, the first thing that must be understood is their primary function and even required. The primary function of grounding rings or grounding electrodes is to provide the required SG connection when an unlined metal process pipe is not available.
A grounding ring is a metallic ring that is placed around the process pipe to provide a low-impedance path to ground. The ring is typically made of copper or stainless steel and is installed between the flanges of the flow meter and the process pipe. The grounding ring is connected to the flow meter and to an earth ground to provide a continuous path for any induced electrical currents to flow.
Grounding rings are commonly used in applications where the process fluid is conductive, such as in water treatment, chemical processing, and mining. They are relatively easy to install and provide a reliable ground connection. They are also effective at reducing the effects of electromagnetic interference (EMI) and radio frequency interference (RFI) on the flow meter.

Figure 2. Typical wafer-style magmeter flowtube with supplied SG wires installed in flanged metal process pipe.
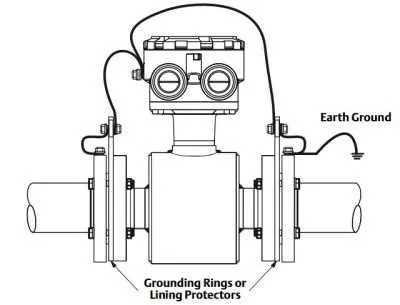
Figure 3. Flanged-style magmeter flowtube with SG grounding straps and rings installed in nonmetallic pipe.
A grounding electrode is a metal rod or plate that is driven into the ground to provide a low-impedance path to earth. The electrode is connected to the flow meter to provide a direct ground connection. Grounding electrodes are commonly used in applications where the process fluid is non-conductive, such as in oil and gas production, food and beverage processing, and pharmaceutical manufacturing.
Grounding electrodes are effective at providing a stable ground connection in non-conductive environments. However, they may be less effective at reducing the effects of EMI and RFI on the flow meter.
Contact us to determine which flow tube models are available with grounding rings and grounding electrodes.

Magnetic flowmeter systems are often preferred for hazardous process liquid applications due to their availability in numerous liner and electrode material choices. This provides compatibility with many hazardous chemicals, making them a safer option.
If grounding rings or electrodes are required, they should be made from the same material as the measuring electrode to ensure chemical compatibility with the process liquid. This is crucial to avoid potential damage to the electrode and the system as a whole.
In such applications, the adjacent process piping is usually nonmetallic or lined. Grounding electrodes can offer substantial cost savings over grounding rings made from exotic materials, as the latter are more expensive. Additionally, grounding electrodes are easier to install and have fewer leak-points, further increasing their cost-effectiveness.
In conclusion, the availability of numerous liner and electrode material choices makes magnetic flowmeter systems a safer option for hazardous process liquid applications. When grounding rings or electrodes are required, they should be made from the same material as the measuring electrode, and grounding electrodes can be a cost-effective alternative to grounding rings.

Does the Magnetic Flowmeter Need 1 or 2 Grounding Rings?
In the past, it was standard practice to use two grounding rings for magnetic flow meters. However, with the development of intelligent microprocessor-based transmitters, only one grounding ring is now required. This not only saves on material costs, but also simplifies the installation process.
Although legacy magnetic flow transmitters still require two grounding rings, modern transmitters can achieve the same level of accuracy and zero stability with just one. The grounding ring is typically installed on the upstream side of the flow tube, providing a solution ground and protecting the liner of the flow tube from moderate abrasion.
In summary, while two grounding rings were once necessary for magnetic flow meters, current technology has made one grounding ring sufficient for achieving accuracy and stability. This advancement has reduced material costs and made installation easier.
How Magnetic flowmeter Flowtube Installation Affects the Solution Ground
Proper installation of flow tubes is essential for accurate SG connection in magnetic flow meters. In the case of metal process piping, correctly installed flow tubes eliminate the need for additional solution grounding rings or electrodes. However, nonmetallic pipe or liner configurations require a solution ground method, and great care must be taken with grounding ring or electrode connections and placement. Below are some tips for achieving proper SG connections to the magnetic flow transmitter.
SG Connection with Metal Process Pipe Flanged-style flow tubes: The most common way to pass the SG connection from the process onto the magnetic flow tube’s body/case is by using flanged, unlined, metal process pipe bolted to a flanged magnetic flow tube (Figure 1). When the metal flanges on each side of the magnetic flow tube are bolted to the magnetic flow tube’s metal flanges, the SG connection is made, and it passes onto the magnetic flow tube’s body/case, eventually reaching the magnetic flow transmitter. Grounding rings or electrodes are not required in this metal-to-metal installation scenario.
Wafer-style flow tubes: Wafer-style flow tubes do not have flanges of their own. Therefore, when mounting a wafer-style magnetic flow tube between flanged, unlined, metal process piping, use the supplied SG wires that ship with the flow tube to connect to the metal process pipe flanges on each side of the wafer flow tube (Figure 2). In this installation scenario, grounding rings are not required. Note that grounding electrodes are not available on wafer-style magnetic flow tubes, and the supplied wires must be used.
SG Connections with Nonmetallic/Plastic/PVC/Lined Process Pipe Flanged-style flow tubes: When flanged-style flow tubes are mounted between nonmetallic, plastic, PVC or lined process piping, the SG must be passed to the flow tube’s body/case through a different path than the process piping flange bolts. In such installation scenarios, use either grounding rings or grounding electrodes (Figure 6).

The correct installation of the flow tube is essential to ensure accurate signal grounding (SG) in electromagnetic flow meters. For metal process piping, correctly installing the flow tube means that additional solution grounding rings or electrodes are not required. However, for nonmetallic pipe or liner configurations, careful attention must be paid to grounding ring or electrode connections and placement. The Electromagnetic Flow Meter can use traditional orifice plate-style grounding rings or Type E grounding rings, which attach to the flow tube’s body/case using grounding straps, wires, or customer-supplied bolts.
To pass the SG from the process onto the flow tube’s body/case, grounding straps or wires must be used for Type C grounding rings. For Type E grounding rings, customer-supplied bolts are used. In lined process pipe configurations, Type E and Type C grounding rings are used in slightly different ways.
For wafer-style flow tubes, grounding rings are required, and the attached SG connection wires must be connected to the grounding rings to pass the SG onto the flow tube’s body/case. The proper SG connection configuration is critical to providing a stable zero flow measurement and achieving accurate flow rate measurements. Without a properly installed solution grounding method, confidence in the flow rate measurement will be diminished.