What is Pressure Measurement?
In industrial settings, pressure measurement is critical for the safe and efficient operation of equipment and processes. Along with flow, level, and temperature, it is one of the four most important measurements in plant operations. Of these four measurements, pressure is often considered the most fundamental and common. By measuring pressure, engineers and operators can infer other key measurements such as flow, level, density, and weight, and make important decisions about how to control their processes. The old adage “If you cannot measure it, you cannot control it” rings true for pressure measurement, as accurate and reliable data is essential for maintaining safe and efficient plant operations. In this blog, we will discuss the basics of pressure measurement, the different types of pressure sensors, and how to select the right sensor for your application.
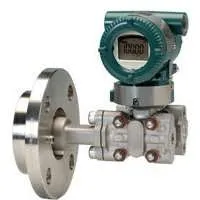
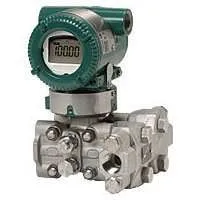
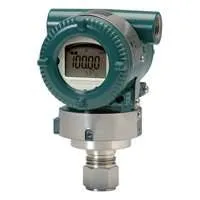
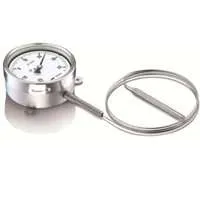
The pressure is the primary measure element for each of these types of transmitters. The flow transmitter, liquid level transmitter, and pressure thermometer use the measured pressure to infer another process parameter.
Physics behind Pressure Measurements
When gas or a liquid is contained within a closed container, their molecules are in a constant, but random motion, constantly colliding with each other as well as with the container walls. All of these collisions occur over a given area combined to result in a force. This force over a defined area is referred to as pressure.
Basically…
P = F/A ; P = Pressure, F = Force, A =Area
In the 1600s, Blaise Pascal developed his principle of transmission of fluid-pressure or more commonly known as Pascal’s Law. This law states that a change in the pressure within the closed vessel will be conveyed equally in every direction within the vessel. Therefore, the pressure within the vessel can be measured from any point within the vessel.
Volume Increases = Pressure Decreases
While in the 1600s, Robert Boyle discovered a new law through experimentation.
Boyle’s Law states that as the volume of the container increases, the pressure decreases. The gas expands to fill the volume available.
Temperature Increases = Pressure Decreases
Jacques Charles first described Charles’ Law in an unpublished work in the 1780s. If the container sizes remain the same, Charles’ Law states that a change in temperature of the container’s contents will directly affect the pressure in the container. As temperature increases in the container, the pressure of the container increases.
Pressure Reference
In industrial pressure measurement, there are four commonly used references: Gauge Pressure, Absolute Pressure,
Differential Pressure, and Vacuum Pressure. These references supply a pressure point in which to compare a pressure.
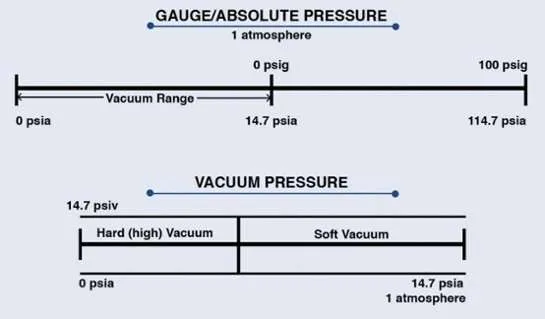
Gauge Pressure
Gauge Pressure use ambient atmospheric pressure as the reference pressure, and the gauge pressure transmitters have a small reference port to sample the ambient atmospheric pressure. With the real-time sampling of this reference, today’s highly accurate pressure transmitters can be affected by local atmospheric pressure changes. The gauge pressure reading can be either negative or positive, depending on whether it increases or decreases over the ambient atmospheric reference. The letter ‘g’ represents Gauge Pressure in the unit of measure (i.e., barg or kpag). Tire pressure is a typical gauge pressure measurement that everyone comes in contact with. While the tire pressure is a gauge pressure measurement that compares the pressure in the tire to the atmospheric pressure. Example of industrial applications: open tank level, line pressure, the blanket pressure in a tank
Absolute Pressure or Compound Pressure
Absolute Pressure uses perfect vacuum pressure (absolute zero) as a reference. All absolute pressure measurements are positive. Although absolute pressure transmitters are not affected by changes in the local atmospheric pressure, absolute pressure typically more expensive than gauge pressure transmitters. Letter ‘a’ or the abbreviation ‘abs’ represents absolute pressure in the measuring unit (i.e. in H2O (abs) or Kpaa). Example of industrial applications: line pressure, open tank level the blanket pressure in a wet/dry tank, plant atmospheric reference.
Compound pressure could be a term that is always equivalent to Absolute Pressure, while the reference of Compound pressure is Ambient Pressure.
Differential Pressure (DP)
Differential Pressure (DP) is the difference between the two pressures. Differential pressure transmitters compare the low-side pressure and high-side pressure as the reference point. The DP Transmitter is marked high-side and low-side, while the DP reading can be either negative or positive depending on whether the low-side or high-side is the larger value. A DP transmitter can be used as a gauge pressure transmitter if the low-side is left open to the atmosphere.
Vacuum Pressure
Vacuum Pressure is the pressure between absolute zero pressure and atmospheric pressure. The standard defined reference is absolute zero pressure, but different companies, industries, and engineers define the reference point differently. If you have an instrument data sheet that uses the word vacuum, have the issuing company define their use of the word vacuum.